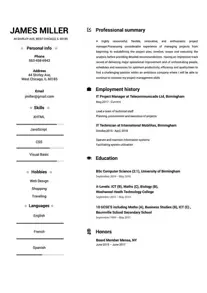
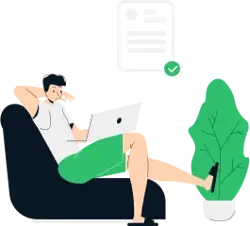
Build your resume in 15 minutes
Create an awesome resume that meets the expectations of potential employers with our selection of professional, field-tested resume templates.
line leader: Resume Samples & Writing Guide
davis_pauline@outlook.com
812-983-5841
Employment history
- Prepare and review reports and documents
- Respond to customer inquiries and complaints
- Provide guidance and direction to staff
- Prepare and review reports and documents
- Establish work schedules and assign specific duties
- Provide guidance and direction to staff
- Establish work schedules and assign specific duties
- Supervise and coordinate the work of administrative and clerical staff
- Handle administrative requests and queries
Education
Skills
Do you already have a resume? Use our PDF converter and edit your resume.
neilallen@inbox.com
961-898-2831
Professional Summary
Employment history
- Ensure accuracy and quality of work
- Perform other duties as assigned
- Respond to customer inquiries and complaints
- Ensure accuracy and quality of work
- Maintain filing systems and records
- Establish work schedules and assign specific duties
- Respond to customer inquiries and complaints
- Perform other duties as assigned
- Maintain filing systems and records
Education
Skills
wilson.bernie@protonmail.com
999-653-8030
Employment history
- Supervise and coordinate the work of administrative and clerical staff
- Establish work schedules and assign specific duties
- Prepare and review reports and documents
- Prepare and review reports and documents
- Train and mentor staff in administrative procedures
- Monitor workflow and ensure deadlines are met
- Prepare and review reports and documents
- Maintain filing systems and records
- Monitor office supplies and place orders when necessary
Education
Skills
francisfoster@outlook.com
817-799-5997
Professional Summary
Employment history
- Maintain filing systems and records
- Establish work schedules and assign specific duties
- Monitor workflow and ensure deadlines are met
- Handle administrative requests and queries
- Ensure accuracy and quality of work
- Monitor office supplies and place orders when necessary
- Monitor office supplies and place orders when necessary
- Supervise and coordinate the work of administrative and clerical staff
- Establish work schedules and assign specific duties
Education
Skills
tony_foster@inbox.com
965-254-8753
Employment history
- Ensure compliance with company policies and procedures
- Train and mentor staff in administrative procedures
- Supervise and coordinate the work of administrative and clerical staff
- Provide guidance and direction to staff
- Perform other duties as assigned
- Monitor workflow and ensure deadlines are met
- Establish work schedules and assign specific duties
- Ensure accuracy and quality of work
- Monitor and evaluate staff performance and provide feedback
Education
Skills
Not in love with this template? Browse our full library of resume templates
line leader Job Descriptions; Explained
If you're applying for an line leader position, it's important to tailor your resume to the specific job requirements in order to differentiate yourself from other candidates. Including accurate and relevant information that directly aligns with the job description can greatly increase your chances of securing an interview with potential employers.
When crafting your resume, be sure to use action verbs and a clear, concise format to highlight your relevant skills and experience. Remember, the job description is your first opportunity to make an impression on recruiters, so pay close attention to the details and make sure you're presenting yourself in the best possible light.
line leader
- Designed safety training programs and trained new employees.
- Sorted, graded, weighed and inspected products and actively monitored production.
- Regulated machine flow, speed, and temperature and stopped and reset machine to address malfunctions..
- Reported malfunctions and errors to supervising staff, addressed concerns and supported other machine operators completing challenging workloads under tight schedules.
- Observed machine operations to verify quality and conformity of packaged products, stepping in to resolve issues promptly and avoid costly production errors.
- Sorted and weighed products after packaging to assess quality, identify defects and grade resulting items.
- Supervised material flow, storage and global order fulfillment.
line leader
- Lead a team of associates in the completion of daily production goals.
- Give instruction to line workers to maximize quality and productivity.
- Complete paperwork and any associated administrative tasks related to the production line.
- Assign tasks based on what orders have come in and which members of the team are working on each day.
- Identify problems and find ways to resolve them so that deadlines are still met without compromising quality.
- Ensure that all members of the team follow company policies and that healthy and safety regulations are being enforced to meet safety compliance.
- Motivate their team and show support and guidance when necessary.
line leader
- Made sure other line members stayed on task and worked at an efficient pace.
- Bagging wood chips and chuncks
- Sealing bags
- Packing bags into boxes
line leader
- Give orders and instructions to assembly line workers so that each member of the production line is aware of what they need to do and what they’re responsible for to maximize quality and productivity.
- Complete paperwork and any associated administrative tasks related to the production line, from updating records to show what’s been completed to noting any issues.
- Quickly identify the cause of problems occur in production line in order to resolve it and meet the deadlines
- Prepare materials needed for the line insure all issued materials are correct for the production.
line leader
- Arrange manpower package.
- Schedule machine package convention
- CNC machine troubleshooting
- Visit customer side
line leader Job Skills
For an line leader position, your job skills are a key factor in demonstrating your value to the company and showing recruiters that you're the ight fit for the role. It's important to be specific when highlighting your skills and ensure that they are directly aligned with the job requirements, as this can greatly improve your chances of being hired. By showcasing your relevant skills and experience, you can make a compelling case for why you're the best candidate for the job.
How to include technical skills in your resume:
Technical skills are a set of specialized abilities and knowledge required to perform a particular job
effectively. Some examples of technical skills are data analysis, project management, software proficiency,
and programming languages, to name a few.
Add the technical skills that will get hired in your career
field with our simple-to-use resume builder. Select your desired resume template, once you reach the skills
section of the builder, manually write in the skill or simply click on "Add more skills". This will
automatically generate the best skills for your career field, choose your skill level, and hit "Save &
Next."
- Data Entry
- Word Processing
- Office Management
- Filing
- Data Analysis
- Spreadsheet Creation
- Typing
- Scheduling
- Record Keeping
- Inventory Management
- Document Management
- Customer Service
- Database Management
- Problem Solving
- Time Management
- Multi-tasking
- Teamwork
- Documentation
- Financial Management
- Microsoft Office
- Copywriting
How to include soft skills in your resume:
Soft skills are non-technical skills that relate to how you work and that can be used in any job. Including
soft skills such as time management, creative thinking, teamwork, and conflict resolution demonstrate your
problem-solving abilities and show that you navigate challenges and changes in the workplace
efficiently.
Add competitive soft skills to make your resume stand-out to recruiters! Simply select
your preferred resume template in the skills section, enter the skills manually or use the "Add more skills"
option. Our resume builder will generate the most relevant soft skills for your career path. Choose your
proficiency level for each skill, and then click "Save & Next" to proceed to the next section.
- Communication
- Interpersonal
- Leadership
- Time Management
- Problem Solving
- Decision Making
- Critical Thinking
- Creativity
- Adaptability
- Teamwork
- Organization
- Planning
- Public Speaking
- Negotiation
- Conflict Resolution
- Research
- Analytical
- Attention to Detail
- Self-Motivation
- Stress Management
- Collaboration
- Coaching
- Mentoring
- Listening
- Networking
- Strategic Thinking
- Negotiation
- Emotional Intelligence
- Adaptability
- Flexibility
- Reliability
- Professionalism
- Computer Literacy
- Technical
- Data Analysis
- Project Management
- Customer Service
- Presentation
- Written Communication
- Social Media
- Troubleshooting
- Quality Assurance
- Collaboration
- Supervisory
- Risk Management
- Database Management
- Training
- Innovation
- Documentation
- Accounting
- Financial Management
- Visualization
- Reporting
- Business Acumen
- Process Improvement
- Documentation
- Relationship Management.
How to Improve Your line leader Resume
Navigating resume pitfalls can mean the difference between landing an interview or not. Missing job descriptions or unexplained work history gaps can cause recruiters to hesitate. Let's not even talk about the impact of bad grammar, and forgetting your contact info could leave your potential employer hanging. Aim to be comprehensive, concise, and accurate.
Employment history
- Provide guidance and direction to staff
- Develop and implement administrative procedures and processes
- Establish work schedules and assign specific duties
- Ensure compliance with company policies and procedures
- Monitor office supplies and place orders when necessary
- Respond to customer inquiries and complaints
- Provide guidance and direction to staff
- Ensure compliance with company policies and procedures
- Prepare and review reports and documents
Education
Skills
Provide your Contact Information and Address Year Gaps
Always explain any gaps in your work history to your advantage.
Key Insights- Employers want to know what you've accomplished, so make sure to explain any gaps using a professional summary.
- Adding extra details and context to explain why you have a gap in your work history shows employers you are a good fit for the position.
How to Optimize Your line leader Resume
Keep an eye out for these resume traps. Neglecting to detail your job roles or explain gaps in your career can lead to unnecessary doubts. Grammar blunders can reflect negatively on you, and without contact information, how can employers reach you? Be meticulous and complete.
virginia-jones@yandex.com
629-153-8613
Professional Summary
Employment history
- Mointor workflow and ensure deadlines are meet
- Mointor office supplies and place orders when neccessary
- Prepare and reviw reports and documents.
- Provide guidiance and direction too staff
- Monitor workflow and ensuer deadlines are met
- Prepair and review reports and doccuments
- "I went to the store to buy some food
- I went too the store too buy some food.
Education
Skills
Include Job Descriptions and Avoid Bad Grammar
Avoid sending a wrong first impression by proofreading your resume.
Key Insights- Spelling and typos are the most common mistakes recruiters see in resumes and by simply avoiding them you can move ahead on the hiring process.
- Before submitting your resume, double check to avoid typos.
line leader Cover Letter Example
A cover letter can be a valuable addition to your job application when applying for an line leader position. Cover letters provide a concise summary of your qualifications, skills, and experience, also it also gives you an opportunity to explain why you're the best fit for the job. Crafting a cover letter that showcases your relevant experience and enthusiasm for the Accounts Payable role can significantly improve your chances of securing an interview.
Davis davis_pauline@outlook.com
812-983-5841
391 Sunset St., Absecon, NJ
08201
UnitedHealth Group
Minnetonka, Minnesota
Dear Hiring Committee
I am a highly motivated and experienced Line Leader with 6 years of experience in Administrative & Clerical. I am excited to apply for the Senior Line Leader position at UnitedHealth Group, where I am confident that I can contribute to your organization's success.
As someone who has faced challenges in various areas of my life and has overcome them, I am confident in my ability to adapt and thrive in any environment. I have developed a reputation for being a collaborative team player and an effective problem solver, which has been instrumental in my career's success. With my experience and passion for Administrative & Clerical, I am excited to apply my skills to this role and contribute to your organization's growth and success.
I am elated about the opportunity to join a team that shares my passion for this field, and values collaboration and innovation. I am confident that together we can overcome whatever tests and challenges are put on our way.
Thank you for your time and consideration,
Pauline Davis
812-983-5841
davis_pauline@outlook.com
Pauline Davis
Showcase your most significant accomplishments and qualifications with this cover
letter.
Personalize this cover letter in just few minutes with our user-friendly tool!
Related Resumes & Cover Letters
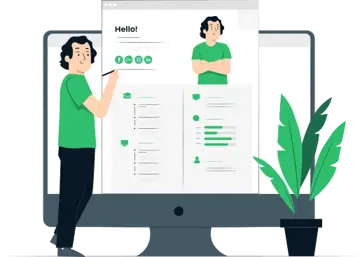
Build your Resume in 15 minutes
Create an awesome resume that meets the expectations of potential employers with our selection of professional, field-tested resume templates.