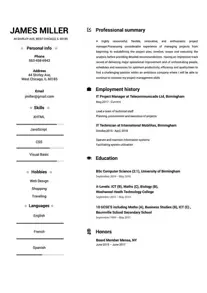
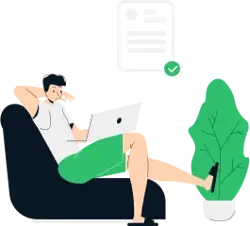
Build your resume in 15 minutes
Create an awesome resume that meets the expectations of potential employers with our selection of professional, field-tested resume templates.
supply chain manager: Resume Samples & Writing Guide
cartertony11@protonmail.com
928-217-2576
Employment history
- Establish and maintain relationships with vendors and suppliers
- Oversee the movement of goods from suppliers to customers in a timely and cost-efficient manner
- Ensure compliance with applicable laws and regulations
- Oversee the movement of goods from suppliers to customers in a timely and cost-efficient manner
- Negotiate contracts with vendors and suppliers to ensure cost-effective solutions
- Develop and implement strategies to reduce supply chain costs
- Develop and implement strategies to reduce supply chain costs
- Monitor and assess customer service levels to ensure customer satisfaction
- Develop and manage budgets for supply chain operations
Education
Skills
Do you already have a resume? Use our PDF converter and edit your resume.
calsmith45@aol.com
688-378-3659
Employment history
- Establish and maintain relationships with vendors and suppliers
- Utilize software to track and monitor performance metrics
- Develop and implement supply chain strategies to improve efficiency, quality, and customer service
- Develop and manage budgets for supply chain operations
- Negotiate contracts with vendors and suppliers to ensure cost-effective solutions
- Manage inventory control, warehousing, and distribution operations
- Monitor and assess customer service levels to ensure customer satisfaction
- Coordinate with other departments to ensure timely and accurate delivery of goods
- Monitor and analyze supply chain performance metrics and suggest areas of improvement
Education
Skills
tombailey2@yandex.com
738-680-3402
Professional Summary
Employment history
- Analyze data to identify trends and opportunities for improvement
- Establish and maintain relationships with vendors and suppliers
- Develop and implement supply chain strategies to improve efficiency, quality, and customer service
- Track and report on inventory levels, delivery times, and transportation costs
- Oversee the movement of goods from suppliers to customers in a timely and cost-efficient manner
- Develop and manage budgets for supply chain operations
- Develop and implement supply chain strategies to improve efficiency, quality, and customer service
- Manage inventory control, warehousing, and distribution operations
- Develop and implement strategies to reduce supply chain costs
Education
Skills
taylor_pauline@zoho.com
704-044-0336
Professional Summary
Employment history
- Negotiate contracts with vendors and suppliers to ensure cost-effective solutions
- Coordinate with other departments to ensure timely and accurate delivery of goods
- Monitor and analyze supply chain performance metrics and suggest areas of improvement
- Utilize software to track and monitor performance metrics
- Negotiate contracts with vendors and suppliers to ensure cost-effective solutions
- Develop and manage budgets for supply chain operations
- Manage and coordinate logistics operations, including scheduling, routing, and transportation
- Track and report on inventory levels, delivery times, and transportation costs
- Develop and implement strategies to reduce supply chain costs
Education
Skills
brad-quinn@protonmail.com
958-234-9166
Employment history
- Develop and implement supply chain strategies to improve efficiency, quality, and customer service
- Monitor and assess customer service levels to ensure customer satisfaction
- Coordinate with other departments to ensure timely and accurate delivery of goods
- Utilize software to track and monitor performance metrics
- Monitor and analyze supply chain performance metrics and suggest areas of improvement
- Monitor and assess customer service levels to ensure customer satisfaction
- Utilize software to track and monitor performance metrics
- Develop and manage budgets for supply chain operations
- Analyze data to identify trends and opportunities for improvement
Education
Skills
Not in love with this template? Browse our full library of resume templates
supply chain manager Job Descriptions; Explained
If you're applying for an supply chain manager position, it's important to tailor your resume to the specific job requirements in order to differentiate yourself from other candidates. Including accurate and relevant information that directly aligns with the job description can greatly increase your chances of securing an interview with potential employers.
When crafting your resume, be sure to use action verbs and a clear, concise format to highlight your relevant skills and experience. Remember, the job description is your first opportunity to make an impression on recruiters, so pay close attention to the details and make sure you're presenting yourself in the best possible light.
supply chain manager
- Warehouse performance monitoring
- Customer service improvement & cost control
- Maximize stock benefits
- Budget preparation & control
- Change management & SOP setup
supply chain manager
- Was responsible for supply chain activities of company from 5 Manufacturing Plants in Meerut (UP) and 1 Manufacturing Plant in Lucknow (UP), 2 Company Owner Depots (1 in Muzaffarpur, Bihar and 1 in Nashik (Maharashtra). Was also responsible for Inbound Logistics in seeds from South (Bellary and Hyderabad).
- Resolve problems concerning transportation, logistics systems, and Customer Service.
- Negotiate with customers to improve supply chain efficiency or sustainability.customer issues.
- Represent the company in negotiating contracts and formulating policies with suppliers.
supply chain manager
- Developed better customer relationship and service.
- Created better delivery mechanisms for products and services in demand with minimum delay.
- Improvised productivity and business functions.
- Minimized warehouse and transportation costs.
- Minimized direct and indirect costs.
- Assisted in achieving the shipping of the right products to the right place at the right time.
- Enhanced inventory management, supporting the successful execution of just-in-time stock models.
supply chain manager
- CUSTOMER SERVICE: Coordinate all supply chain services within Brazil area such as material planning, scheduling, and strict inventory control for immediate availability; Order Intake processing; checking out the consistent dates of delivery/transit time/destination; prepared and analyzed schedules as customer service department to maintain high customer satisfaction by keeping the representatives notified of any service issues; Reviewed purchasing decisions, orders and vendor contracts to ensure requests are met in a timely manner. Address and resolve all order discrepancies immediately to ensure quality and maintain the organization’s reputation; Analyzed cost and appropriate shipping arrangements and arranged deliveries; Assisted and provided support to the sales manager.
- IMPORTS/EXPORTS: Responsible for importing RFID tags from Thailand, USA and Germany to supply South America’s market; Coordinated transportation of products from country of origin to final destination for both air and ocean; Created, prepared and reviewed export documents (Commercial Invoices, Packing List, L/C, SLI’s, SED’s, Licenses, Certificate of Origin etc); Knowledge of Incoterms (International Commercial Terms); Cleared customs, invoiced and prepared monthly reporting of operations; Created tracking reports, decreasing customer inquiries and optimizing time savings; Worked closely with overseas staff in regards to ordering samples, placing factory orders, receiving vendor quotes, reviewing Letters of Credits and logistics.
- STOCK: Developed and implemented effective inventory controls, eliminating shortage to improve rapport with outside vendors.
- Participate in the development products.
supply chain manager
- Building and maintaining vendor relationships – Closely working with up to 70 vendors, 5 large scale distributors and up to 5 Contract manufacturing firms (Electronic assembly). SC through put cycle time down by 12%
- Analysis and identification of savings across all departments and segments. 20% of year-over year savings of Procurement budget
- Development, deployment, and ongoing enhancement of supply and demand planning – utilizing internal company systems. Increased forecast accuracy by 10%
- Oversaw a companywide transformation from MTO strategy to MTS – Fill rate increase from 10% to 60% within the first year (2019 target is 90%)
- Management of contract manufactures – Closely working with project managers to develop and maintain assembly schedule to meet delivery targets – 90% on time Customer delivery (up 15%)
- Inventory management – Analyzing inventory MOQs and current inventory levels daily while maintaining an ongoing analysis of inventory to keep costs down and optimal on-hand quantities
- Purchasing – Responsible for yearly purchasing budget of ~$3M. Researching new materials and production methods. Working with finance teams to support P&L reporting and analysis functions
supply chain manager Job Skills
For an supply chain manager position, your job skills are a key factor in demonstrating your value to the company and showing recruiters that you're the ight fit for the role. It's important to be specific when highlighting your skills and ensure that they are directly aligned with the job requirements, as this can greatly improve your chances of being hired. By showcasing your relevant skills and experience, you can make a compelling case for why you're the best candidate for the job.
How to include technical skills in your resume:
Technical skills are a set of specialized abilities and knowledge required to perform a particular job
effectively. Some examples of technical skills are data analysis, project management, software proficiency,
and programming languages, to name a few.
Add the technical skills that will get hired in your career
field with our simple-to-use resume builder. Select your desired resume template, once you reach the skills
section of the builder, manually write in the skill or simply click on "Add more skills". This will
automatically generate the best skills for your career field, choose your skill level, and hit "Save &
Next."
- Inventory Management
- Logistics
- Supply Chain Management
- Warehousing
- Transportation
- Procurement
- Forecasting
- Distribution
- Lean Manufacturing
- Supply Chain Optimization
- Cost Analysis
- Quality Control
- Supply Chain Analytics
- Six Sigma
- Vendor Management
- Production Planning
- Data Entry
- Risk Management
- Negotiation
- Inventory Control
- Shipping/Receiving
How to include soft skills in your resume:
Soft skills are non-technical skills that relate to how you work and that can be used in any job. Including
soft skills such as time management, creative thinking, teamwork, and conflict resolution demonstrate your
problem-solving abilities and show that you navigate challenges and changes in the workplace
efficiently.
Add competitive soft skills to make your resume stand-out to recruiters! Simply select
your preferred resume template in the skills section, enter the skills manually or use the "Add more skills"
option. Our resume builder will generate the most relevant soft skills for your career path. Choose your
proficiency level for each skill, and then click "Save & Next" to proceed to the next section.
- Communication
- Interpersonal
- Leadership
- Time Management
- Problem Solving
- Decision Making
- Critical Thinking
- Creativity
- Adaptability
- Teamwork
- Organization
- Planning
- Public Speaking
- Negotiation
- Conflict Resolution
- Research
- Analytical
- Attention to Detail
- Self-Motivation
- Stress Management
- Collaboration
- Coaching
- Mentoring
- Listening
- Networking
- Strategic Thinking
- Negotiation
- Emotional Intelligence
- Adaptability
- Flexibility
- Reliability
- Professionalism
- Computer Literacy
- Technical
- Data Analysis
- Project Management
- Customer Service
- Presentation
- Written Communication
- Social Media
- Troubleshooting
- Quality Assurance
- Collaboration
- Supervisory
- Risk Management
- Database Management
- Training
- Innovation
- Documentation
- Accounting
- Financial Management
- Visualization
- Reporting
- Business Acumen
- Process Improvement
- Documentation
- Relationship Management.
How to Improve Your supply chain manager Resume
Navigating resume pitfalls can mean the difference between landing an interview or not. Missing job descriptions or unexplained work history gaps can cause recruiters to hesitate. Let's not even talk about the impact of bad grammar, and forgetting your contact info could leave your potential employer hanging. Aim to be comprehensive, concise, and accurate.
Employment history
- Ensure compliance with applicable laws and regulations
- Develop and implement strategies to reduce supply chain costs
- Analyze data to identify trends and opportunities for improvement
- Track and report on inventory levels, delivery times, and transportation costs
- Ensure compliance with applicable laws and regulations
- Develop and manage budgets for supply chain operations
- Oversee the movement of goods from suppliers to customers in a timely and cost-efficient manner
- Develop and implement strategies to reduce supply chain costs
- Utilize software to track and monitor performance metrics
Education
Skills
Provide your Contact Information and Address Year Gaps
Always explain any gaps in your work history to your advantage.
Key Insights- Employers want to know what you've accomplished, so make sure to explain any gaps using a professional summary.
- Adding extra details and context to explain why you have a gap in your work history shows employers you are a good fit for the position.
How to Optimize Your supply chain manager Resume
Keep an eye out for these resume traps. Neglecting to detail your job roles or explain gaps in your career can lead to unnecessary doubts. Grammar blunders can reflect negatively on you, and without contact information, how can employers reach you? Be meticulous and complete.
hal-roberts@yahoo.com
837-158-7885
Employment history
- Negotiate contract's with vendor's and supplier's to ensure cost-effective solution's
- Oversee the movement's of good's from supplier's to customer's in a timely and cost-efficient maner
- Co-ordinate with other department's to ensure timely and accurate delivery of good's
- Track and report on inventry levels, delivery times, an transportation costs
- Develop and manage budget's for supply chain operations
- Co-ordinate with other departments to ensuer timely and accurate delivery of goods
- "I like to eat apples
- and oranges
- I likes to eat apples
- and oranges
Education
Skills
Include Job Descriptions and Avoid Bad Grammar
Avoid sending a wrong first impression by proofreading your resume.
Key Insights- Spelling and typos are the most common mistakes recruiters see in resumes and by simply avoiding them you can move ahead on the hiring process.
- Before submitting your resume, double check to avoid typos.
supply chain manager Cover Letter Example
A cover letter can be a valuable addition to your job application when applying for an supply chain manager position. Cover letters provide a concise summary of your qualifications, skills, and experience, also it also gives you an opportunity to explain why you're the best fit for the job. Crafting a cover letter that showcases your relevant experience and enthusiasm for the Accounts Payable role can significantly improve your chances of securing an interview.
Carter cartertony11@protonmail.com
928-217-2576
244 Hickory Hill Road, Bishop, TX
78343
FedEx
Memphis, Tennessee
Esteemed Recruitment Team
I am writing to express my interest in the Senior Supply Chain Manager position at FedEx. As a Supply Chain Manager with 10 years of experience in Logistics & Supply Chain myself, I believe I have the necessary skills and expertise to excel in this role.
Growing up, I always had a fascination with Warehouse Management. As I pursued my education and gained experience in this field, I realized that this was where I could make the most impact. I have had the opportunity to work on things throughout my career like personal projects and voluntary work, which have developed in me a deep understanding of the challenges and opportunities in this field. I am excited to bring my passion and expertise to the role at and help your organization achieve its goals.
I appreciate the time and consideration you have given my application. I am confident that if we work together we could achieve great things and so I look forward to the opportunity to join your team.
Sincerely,
Tony Carter
928-217-2576
cartertony11@protonmail.com
Tony Carter
Showcase your most significant accomplishments and qualifications with this cover
letter.
Personalize this cover letter in just few minutes with our user-friendly tool!
Related Resumes & Cover Letters
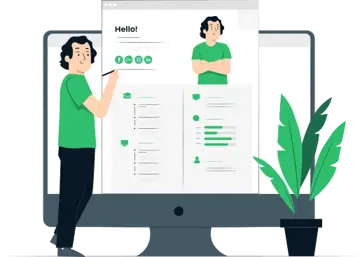
Build your Resume in 15 minutes
Create an awesome resume that meets the expectations of potential employers with our selection of professional, field-tested resume templates.