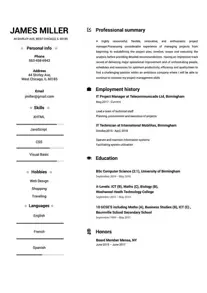
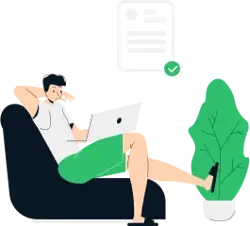
Build your resume in 15 minutes
Create an awesome resume that meets the expectations of potential employers with our selection of professional, field-tested resume templates.
quality assurance manager: Resume Samples & Writing Guide
woodsimon26@hotmail.com
710-947-3820
Professional Summary
Employment history
- Analyze customer requirements and develop test plans accordingly
- Train and mentor junior quality assurance engineers
- Participate in code reviews and design reviews
- Monitor and analyze quality assurance metrics to identify trends and make recommendations for improvement
- Design and implement test automation frameworks and tools
- Train and mentor junior quality assurance engineers
- Monitor and report on software quality assurance activities
- Create and maintain test data and test environments
- Participate in code reviews and design reviews
Education
Skills
Do you already have a resume? Use our PDF converter and edit your resume.
lewisyolie@icloud.com
786-015-8824
Employment history
- Develop and execute test plans and test cases to ensure the quality of software applications
- Document and track software defects
- Design and implement test automation frameworks and tools
- Collaborate with software development teams to ensure quality throughout the development lifecycle
- Create and maintain test data and test environments
- Analyze customer requirements and develop test plans accordingly
- Design and implement test automation frameworks and tools
- Develop and execute test plans and test cases to ensure the quality of software applications
- Monitor and report on software quality assurance activities
Education
Skills
kellyvincent@aol.com
737-760-2032
Professional Summary
Employment history
- Perform manual and automated software testing
- Participate in code reviews and design reviews
- Document and track software defects
- Participate in code reviews and design reviews
- Troubleshoot and debug software applications
- Monitor and report on software quality assurance activities
- Develop and execute test plans and test cases to ensure the quality of software applications
- Train and mentor junior quality assurance engineers
- Monitor and analyze quality assurance metrics to identify trends and make recommendations for improvement
Education
Skills
adam_foster@aol.com
762-420-3943
Employment history
- Develop and execute test plans and test cases to ensure the quality of software applications
- Provide feedback and recommendations on software usability and functionality
- Analyze customer requirements and develop test plans accordingly
Education
Skills
kingxaviero@icloud.com
829-023-5030
Professional Summary
Employment history
- Monitor and analyze quality assurance metrics to identify trends and make recommendations for improvement
- Research and recommend new technologies and best practices for testing
- Document and track software defects
- Participate in code reviews and design reviews
- Provide feedback and recommendations on software usability and functionality
- Monitor and report on software quality assurance activities
- Perform manual and automated software testing
- Monitor and analyze quality assurance metrics to identify trends and make recommendations for improvement
- Design and implement test automation frameworks and tools
Education
Skills
Not in love with this template? Browse our full library of resume templates
quality assurance manager Job Descriptions; Explained
If you're applying for an quality assurance manager position, it's important to tailor your resume to the specific job requirements in order to differentiate yourself from other candidates. Including accurate and relevant information that directly aligns with the job description can greatly increase your chances of securing an interview with potential employers.
When crafting your resume, be sure to use action verbs and a clear, concise format to highlight your relevant skills and experience. Remember, the job description is your first opportunity to make an impression on recruiters, so pay close attention to the details and make sure you're presenting yourself in the best possible light.
quality assurance manager
- Interpreted, build upon, and comply with company quality assurance standards
- Carefully maintained complaint and nonconformance processing through records and tracking systems, including root cause and corrective actions
- Documented quality assurance activities with internal reporting and audits
- Developed new standards for production and design, with improvements as needed, and created testing protocols for implementation across all service lines
- Identified training needs and take action to ensure company-wide compliance
- Pursued continuing education on new solutions, technology, and skills
quality assurance manager/lead auditor
- Ensure that customer requirements, statutory regulations and internal requirements are enforced by the inspectors and internal auditors.
- Manage Repair and Manufacturing inspectors- Manage internal auditors.
- Main contact for Customer’s , 3rd party and regulatory audits.
- Responsible for creating internal audits schedules in accordance with external/internal requirements and company needs
quality assurance manager
- Instrumental in the development of the Quality Management plan for the Integrated Computerized Tax Administration System (ICTAS) for the Jamaica Tax Administration Reform Project (TAXARP).
- Trained Quality Assurance Analysts in Information Systems Auditing Tools and Techniques
- Developed and implemented Fiscal Services’ quality assurance strategic plan and department’s budget.
- Led a team of Business Analysts, Quality Assurance Analysts and users in the sucessfull testing and implementation of the system for the issuance of the Taxpayer Registration Number(TRN)
quality assurance manager
- Responsible for the Batch release for sale after reviewing the Batch Manufacturing & Packaging Records, In-process Quality Control & Finished product analysis reports.
- Responsible for review, approval & authorisation of the system for review, approval, distribution, revision and destruction of SOPs and other controlled documents.
- Responsible for review and approval of SOPs, Work Instructions, General Test Procedures, Product Specifications and Methods of Analysis.
- Responsible for the review and approval of key documents such as Quality Manual, Annual Product Quality Review, Batch manufacturing and Packaging records, Process Validation, Analytical Method Validations, Equipment Qualifications, Validation Master Plan, Stability Reports etc.
- Responsible for handling of Market Complains, Product Recalls, Change Controls, Deviations, NCR, Incidents, CAPA, OOS and OOTs etc.
- Responsible for conducting Root Cause Analysis to remedy Deviations having negative impact on Product Quality.
- Responsible for the development & approval of Artworks.
quality assurance manager
- Evaluate calls to avoid errors.
- Audit certain number of calls to maintain professionalism and to better communication between agents and customer.
- Manages projects to improve product quality with direction
- Manage and assist pre-production samples meetings and approval process in APAC
quality assurance manager Job Skills
For an quality assurance manager position, your job skills are a key factor in demonstrating your value to the company and showing recruiters that you're the ight fit for the role. It's important to be specific when highlighting your skills and ensure that they are directly aligned with the job requirements, as this can greatly improve your chances of being hired. By showcasing your relevant skills and experience, you can make a compelling case for why you're the best candidate for the job.
How to include technical skills in your resume:
Technical skills are a set of specialized abilities and knowledge required to perform a particular job
effectively. Some examples of technical skills are data analysis, project management, software proficiency,
and programming languages, to name a few.
Add the technical skills that will get hired in your career
field with our simple-to-use resume builder. Select your desired resume template, once you reach the skills
section of the builder, manually write in the skill or simply click on "Add more skills". This will
automatically generate the best skills for your career field, choose your skill level, and hit "Save &
Next."
- Test Automation
- Debugging
- Java
- JavaScript
- Automation Testing
- SQL
- C++
- Agile Methodologies
- Software Development Life Cycle
- Quality Assurance
- HTML
- CSS
- API Testing
- Unit Testing
- Software Testing
- Performance Testing
- Mobile Testing
- Regression Testing
- Security Testing
- Integration Testing
How to include soft skills in your resume:
Soft skills are non-technical skills that relate to how you work and that can be used in any job. Including
soft skills such as time management, creative thinking, teamwork, and conflict resolution demonstrate your
problem-solving abilities and show that you navigate challenges and changes in the workplace
efficiently.
Add competitive soft skills to make your resume stand-out to recruiters! Simply select
your preferred resume template in the skills section, enter the skills manually or use the "Add more skills"
option. Our resume builder will generate the most relevant soft skills for your career path. Choose your
proficiency level for each skill, and then click "Save & Next" to proceed to the next section.
- Communication
- Interpersonal
- Leadership
- Time Management
- Problem Solving
- Decision Making
- Critical Thinking
- Creativity
- Adaptability
- Teamwork
- Organization
- Planning
- Public Speaking
- Negotiation
- Conflict Resolution
- Research
- Analytical
- Attention to Detail
- Self-Motivation
- Stress Management
- Collaboration
- Coaching
- Mentoring
- Listening
- Networking
- Strategic Thinking
- Negotiation
- Emotional Intelligence
- Adaptability
- Flexibility
- Reliability
- Professionalism
- Computer Literacy
- Technical
- Data Analysis
- Project Management
- Customer Service
- Presentation
- Written Communication
- Social Media
- Troubleshooting
- Quality Assurance
- Collaboration
- Supervisory
- Risk Management
- Database Management
- Training
- Innovation
- Documentation
- Accounting
- Financial Management
- Visualization
- Reporting
- Business Acumen
- Process Improvement
- Documentation
- Relationship Management.
How to Improve Your quality assurance manager Resume
Navigating resume pitfalls can mean the difference between landing an interview or not. Missing job descriptions or unexplained work history gaps can cause recruiters to hesitate. Let's not even talk about the impact of bad grammar, and forgetting your contact info could leave your potential employer hanging. Aim to be comprehensive, concise, and accurate.
Professional Summary
Employment history
- Create and maintain test data and test environments
- Perform manual and automated software testing
- Develop and maintain quality assurance standards and procedures
- Troubleshoot and debug software applications
- Participate in code reviews and design reviews
- Design and implement test automation frameworks and tools
Education
Skills
Include your Contact Information and Job Descriptions
Missing job descriptions lessens your chances of getting hired.
Key Insights- Employers want to know what you've accomplished, so make sure to include descriptions for all of your previous jobs.
- Keep job descriptions short but don't just list your jobs.
- Never copy-paste a job description to post on your resume. Get inspired and use tools to help you write customized descriptions.
How to Optimize Your quality assurance manager Resume
Keep an eye out for these resume traps. Neglecting to detail your job roles or explain gaps in your career can lead to unnecessary doubts. Grammar blunders can reflect negatively on you, and without contact information, how can employers reach you? Be meticulous and complete.
ernestdavis@aol.com
801-222-3140
Employment history
- Montior and analize quality assurance metrics to identify trends and make recomendations for improvemnet
- Designd and impliment test automation frameworks and tools
- Provied feedback and recomendations on software usabillity and functionallity
- Participate in code reviews and design review's
- Collaborate with software development team's to ensure quality throughout the development lifecycle's
- Monitor and analyze quality assurance metric's to identify trends and make recommendation's for improvement
- Participate in code reviews and design reviews
- Create and maintain test data and test enviroments
- Develop and execute test plans and test cases, to ensue the quality of software applications.
Education
Skills
Correct Grammar and Address Gap Years in Your Resume
Don't leave unexplained gaps in your work history.
Key Insights- When explaining gaps in your employment section, start by being honest.
- Elaborate on the gap and show that you never stopped learning.
- Explain and elaborate any gap in your work history by highlighting new skills.
quality assurance manager Cover Letter Example
A cover letter can be a valuable addition to your job application when applying for an quality assurance manager position. Cover letters provide a concise summary of your qualifications, skills, and experience, also it also gives you an opportunity to explain why you're the best fit for the job. Crafting a cover letter that showcases your relevant experience and enthusiasm for the Accounts Payable role can significantly improve your chances of securing an interview.
Wood woodsimon26@hotmail.com
710-947-3820
951 Hickory Hill Road, Savage, MD
20763
HP
Palo Alto, California
Greetings HP Recruitment Team
I am writing to express my interest in the Senior Quality Assurance Manager position at HP. As a Quality Assurance Manager with 11 years of experience in Software Development myself, I believe I have the necessary skills and expertise to excel in this role.
Throughout my life, I have pursued my passion for Algorithm Design and have gained experience in this field as a result. This experience has given me valuable skills such as Adaptability and Stress Management, which I am excited to bring to this position. I am eager to work with a team that shares my enthusiasm as a Quality Assurance Manager and help your organization achieve its well determined goals.
I appreciate the time and consideration you have given my application. I am confident that if we work together we could achieve great things and so I look forward to the opportunity to join your team.
Looking forward to hearing from you,
Simon Wood
710-947-3820
woodsimon26@hotmail.com
Simon Wood
Showcase your most significant accomplishments and qualifications with this cover
letter.
Personalize this cover letter in just few minutes with our user-friendly tool!
Related Resumes & Cover Letters
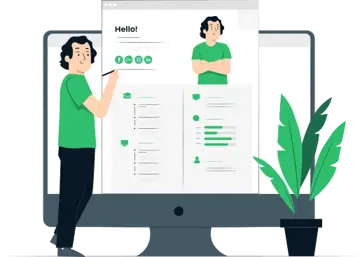
Build your Resume in 15 minutes
Create an awesome resume that meets the expectations of potential employers with our selection of professional, field-tested resume templates.