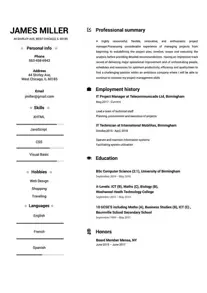
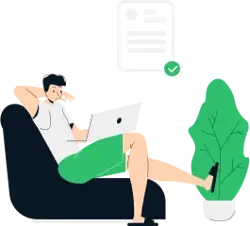
Build your resume in 15 minutes
Create an awesome resume that meets the expectations of potential employers with our selection of professional, field-tested resume templates.
quality assurance supervisor: Resume Samples & Writing Guide
harrisfred7@zoho.com
786-103-0876
Professional Summary
Employment history
- Ensure compliance with regulatory requirements
- Analyze production data and identify areas for improvement
- Analyze customer feedback and take corrective action as necessary
- Investigate customer complaints and take corrective action
- Monitor and evaluate quality assurance systems to ensure they are effective and compliant with industry standards
- Create and maintain records of inspection and test results
- Develop and maintain quality assurance metrics
- Develop and implement quality assurance procedures and standards
- Monitor and evaluate quality assurance systems to ensure they are effective and compliant with industry standards
Education
Skills
Do you already have a resume? Use our PDF converter and edit your resume.
griffin_simon@inbox.com
936-884-0900
Professional Summary
Employment history
- Train and mentor staff in quality assurance processes and procedures
- Monitor and evaluate quality assurance systems to ensure they are effective and compliant with industry standards
- Collaborate with engineering teams to identify and resolve quality issues
- Conduct internal audits to ensure quality standards are met
- Develop and implement quality assurance procedures and standards
- Develop and implement strategies to improve product quality
- Develop and implement quality assurance procedures and standards
- Analyze customer feedback and take corrective action as necessary
- Prepare and present reports on quality assurance activities
Education
Skills
garyscott12@inbox.com
623-055-3305
Employment history
- Develop and implement quality assurance procedures and standards
- Prepare and present reports on quality assurance activities
- Train and mentor staff in quality assurance processes and procedures
- Ensure compliance with regulatory requirements
- Collaborate with engineering teams to identify and resolve quality issues
- Prepare and present reports on quality assurance activities
- Monitor and evaluate quality assurance systems to ensure they are effective and compliant with industry standards
- Monitor and review product performance
- Develop and maintain quality assurance metrics
Education
Skills
ursulawalker42@yahoo.com
796-484-8696
Employment history
- Analyze customer feedback and take corrective action as necessary
- Ensure compliance with regulatory requirements
- Monitor and review product performance
Education
Skills
kyledavis33@hotmail.com
811-082-1291
Employment history
- Oversee the development and implementation of quality control plans
- Analyze customer feedback and take corrective action as necessary
- Develop and implement quality assurance procedures and standards
- Collaborate with engineering teams to identify and resolve quality issues
- Train and mentor staff in quality assurance processes and procedures
- Analyze customer feedback and take corrective action as necessary
- Conduct internal audits to ensure quality standards are met
- Develop and implement strategies to improve product quality
- Prepare and present reports on quality assurance activities
Education
Skills
Not in love with this template? Browse our full library of resume templates
quality assurance supervisor Job Descriptions; Explained
If you're applying for an quality assurance supervisor position, it's important to tailor your resume to the specific job requirements in order to differentiate yourself from other candidates. Including accurate and relevant information that directly aligns with the job description can greatly increase your chances of securing an interview with potential employers.
When crafting your resume, be sure to use action verbs and a clear, concise format to highlight your relevant skills and experience. Remember, the job description is your first opportunity to make an impression on recruiters, so pay close attention to the details and make sure you're presenting yourself in the best possible light.
quality assurance supervisor
- Maintained metrics, reports, process documentation, customer service logs, training, and safety records.
- Supervised the work of logistics specialists, planners, or schedulers.
- Maintained accurate and complete employee records as required by laws or administrative policies.
- Observed and evaluated employee work to determine progress and make suggestions for improvement.
- Instructed employees individually and in groups, using various teaching methods such as lectures, discussions, and demonstrations.
quality assurance supervisor
- Resolve complaints concerning transportation, logistics systems, or customer issues.
- Maintain complaint reports, process documentation, developed training for specific to Virginia Operations Quality Assurance
- Collaborate with other departments to provide resolution to complaints with processes, such as escalations and trip monitoring.
- Supervise the work of Quality Assurance Representatives specialists, planners, or schedulers.
- Conducted annual reviews for employees providing feedback on their performance and recommended salary increases.
quality assurance supervisor
- Clean, maintain, calibrate, or repair measuring instruments or test equipment, such as thermometer, scales, or ph meters.
- Oversaw the onboarding and training of new employees
- Implemented company policies, technical procedures and standards for keeping security of data and personal information safe
- Reviewed phone calls and graded performances
quality assurance supervisor/marketing coordinator
- Managed teams across the State of Michigan, both Admissions Staff and Career Transition Specialists. Direct Human resources activities, including payroll, annual evaluations, and improvement plans. Evaluated WIOA reporting systems, ensured compliance with employment verification’s and documentation collection.
- Empowered individuals to enroll in training and or employment by helping them to understand and overcome personal, social, or behavioral problems affecting their educational or vocational situations.
- Exceeded recruitment expectations by providing qualified candidates, using community resources, networking, internet recruiting resources, media advertisements, job fairs, other High Schools and Training Schools, or candidate referrals.
- Designed and implemented marketing strategies, based on knowledge of establishment objectives, market characteristics, Department of Labor Requirements.
quality assurance supervisor
- Direct and coordinate the activities of employees engaged in the production and inspection of of machined goods.
- Conduct employee training in equipment operations and work and safety procedures, and assign employee training to experienced workers.
- Implement measures to motivate employees and to improve production methods, product quality, and efficiency.
- Inspect products for quality and adherence to customer and licensor specifications.
quality assurance supervisor Job Skills
For an quality assurance supervisor position, your job skills are a key factor in demonstrating your value to the company and showing recruiters that you're the ight fit for the role. It's important to be specific when highlighting your skills and ensure that they are directly aligned with the job requirements, as this can greatly improve your chances of being hired. By showcasing your relevant skills and experience, you can make a compelling case for why you're the best candidate for the job.
How to include technical skills in your resume:
Technical skills are a set of specialized abilities and knowledge required to perform a particular job
effectively. Some examples of technical skills are data analysis, project management, software proficiency,
and programming languages, to name a few.
Add the technical skills that will get hired in your career
field with our simple-to-use resume builder. Select your desired resume template, once you reach the skills
section of the builder, manually write in the skill or simply click on "Add more skills". This will
automatically generate the best skills for your career field, choose your skill level, and hit "Save &
Next."
- Test Automation
- Debugging
- Software Testing
- System Testing
- Agile Methodology
- Automation Testing
- Software Quality Assurance
- Performance Testing
- Quality Assurance Processes
- Regression Testing
- Test Planning
- Test Scripting
- Test Execution
- Test Design
- Test Strategy
- Software Development
- User Acceptance Testing
- Security Testing
- Defect Tracking
- Test Case Design.
How to include soft skills in your resume:
Soft skills are non-technical skills that relate to how you work and that can be used in any job. Including
soft skills such as time management, creative thinking, teamwork, and conflict resolution demonstrate your
problem-solving abilities and show that you navigate challenges and changes in the workplace
efficiently.
Add competitive soft skills to make your resume stand-out to recruiters! Simply select
your preferred resume template in the skills section, enter the skills manually or use the "Add more skills"
option. Our resume builder will generate the most relevant soft skills for your career path. Choose your
proficiency level for each skill, and then click "Save & Next" to proceed to the next section.
- Communication
- Interpersonal
- Leadership
- Time Management
- Problem Solving
- Decision Making
- Critical Thinking
- Creativity
- Adaptability
- Teamwork
- Organization
- Planning
- Public Speaking
- Negotiation
- Conflict Resolution
- Research
- Analytical
- Attention to Detail
- Self-Motivation
- Stress Management
- Collaboration
- Coaching
- Mentoring
- Listening
- Networking
- Strategic Thinking
- Negotiation
- Emotional Intelligence
- Adaptability
- Flexibility
- Reliability
- Professionalism
- Computer Literacy
- Technical
- Data Analysis
- Project Management
- Customer Service
- Presentation
- Written Communication
- Social Media
- Troubleshooting
- Quality Assurance
- Collaboration
- Supervisory
- Risk Management
- Database Management
- Training
- Innovation
- Documentation
- Accounting
- Financial Management
- Visualization
- Reporting
- Business Acumen
- Process Improvement
- Documentation
- Relationship Management.
How to Improve Your quality assurance supervisor Resume
Navigating resume pitfalls can mean the difference between landing an interview or not. Missing job descriptions or unexplained work history gaps can cause recruiters to hesitate. Let's not even talk about the impact of bad grammar, and forgetting your contact info could leave your potential employer hanging. Aim to be comprehensive, concise, and accurate.
Employment history
- Oversee the development and implementation of quality control plans
- Develop and maintain quality assurance metrics
- Develop and implement quality assurance procedures and standards
- Prepare and present reports on quality assurance activities
- Analyze production data and identify areas for improvement
- Monitor and evaluate quality assurance systems to ensure they are effective and compliant with industry standards
Education
Skills
Include your Contact Information and Job Descriptions
Missing job descriptions lessens your chances of getting hired.
Key Insights- Employers want to know what you've accomplished, so make sure to include descriptions for all of your previous jobs.
- Keep job descriptions short but don't just list your jobs.
- Never copy-paste a job description to post on your resume. Get inspired and use tools to help you write customized descriptions.
How to Optimize Your quality assurance supervisor Resume
Keep an eye out for these resume traps. Neglecting to detail your job roles or explain gaps in your career can lead to unnecessary doubts. Grammar blunders can reflect negatively on you, and without contact information, how can employers reach you? Be meticulous and complete.
xavieracampbell@protonmail.com
875-914-5904
Employment history
- Prepeare and prensent reportes on quality assurrance activites.
- Trainnd mentor staff in quality assurance processses and proceddures.
- Deveop annd maintian quallity assurrance metricss.
- Moniter and reveiw product performence.
- Develp annd implement quallity assurrance proceddures annd standarrds.
- Overseeee the developement and implemention of quality controll planss.
- Analise production data and indentify areas for improovment.
- Develp and impplement strategiees too improove product qualitty.
- Conducts internals audits to ensure quality standers are meet.
Education
Skills
Correct Grammar and Address Gap Years in Your Resume
Don't leave unexplained gaps in your work history.
Key Insights- When explaining gaps in your employment section, start by being honest.
- Elaborate on the gap and show that you never stopped learning.
- Explain and elaborate any gap in your work history by highlighting new skills.
quality assurance supervisor Cover Letter Example
A cover letter can be a valuable addition to your job application when applying for an quality assurance supervisor position. Cover letters provide a concise summary of your qualifications, skills, and experience, also it also gives you an opportunity to explain why you're the best fit for the job. Crafting a cover letter that showcases your relevant experience and enthusiasm for the Accounts Payable role can significantly improve your chances of securing an interview.
Harris harrisfred7@zoho.com
786-103-0876
568 Valley Drive, Many Farms, AZ
86538
Microsoft
Redmond, Washington
To the respected Microsoft Recruitment Team
I am a results-driven Quality Assurance Supervisor with 11 years of experience in Engineering. I am excited to submit my application for the Lead Quality Assurance Supervisor role at Microsoft, where I believe I can make a valuable contribution to your team.
As someone who has always been committed to making a positive impact on the world, I have pursued opportunities to contribute to my community through my work wherever I may be. My experience in this field has equipped me with the skills and knowledge necessary to succeed throughout my life and I am confident that they will help me to bring my passion and expertise to your organization and help drive your success.
I cannot stress enough how thrilled I am about the chance to join a team of like-minded individuals who share my values and passion for this amazing field. Thank you for considering my application and I hope for the chance to work together.
Looking forward to hearing from you,
Fred Harris
786-103-0876
harrisfred7@zoho.com
Fred Harris
Showcase your most significant accomplishments and qualifications with this cover
letter.
Personalize this cover letter in just few minutes with our user-friendly tool!
Related Resumes & Cover Letters
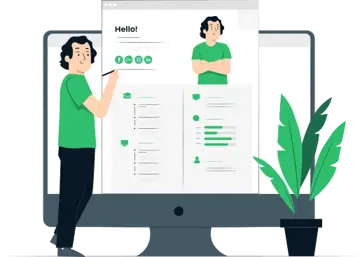
Build your Resume in 15 minutes
Create an awesome resume that meets the expectations of potential employers with our selection of professional, field-tested resume templates.