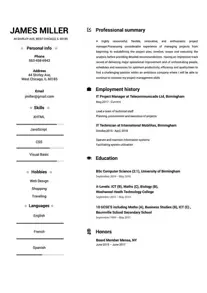
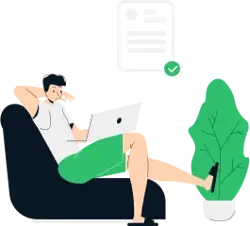
Build your resume in 15 minutes
Create an awesome resume that meets the expectations of potential employers with our selection of professional, field-tested resume templates.
industrial engineer: Resume Samples & Writing Guide
karlgriffin57@aol.com
981-848-8056
Employment history
- Develop and implement safety and environmental policies
- Develop and implement automation systems
- Create and maintain engineering documents, drawings, and specifications
- Develop and implement safety and environmental policies
- Maintain and troubleshoot existing equipment and systems
- Manage and coordinate projects
- Develop and implement process improvements to increase efficiency and reduce costs
- Analyze production processes and recommend improvements
- Manage and coordinate projects
Education
Skills
Do you already have a resume? Use our PDF converter and edit your resume.
normandavis@yahoo.com
782-844-5642
Employment history
- Develop and implement safety and environmental policies
- Perform quality control and assurance tests
- Train and mentor other engineers
- Manage and coordinate projects
- Analyze production processes and recommend improvements
- Develop and implement automation systems
- Analyze production processes and recommend improvements
- Perform quality control and assurance tests
- Develop and implement process improvements to increase efficiency and reduce costs
Education
Skills
kellyoscar39@icloud.com
733-395-9693
Employment history
- Research and evaluate new technologies and equipment
- Monitor and analyze production data to identify trends and areas for improvement
- Analyze production processes and recommend improvements
- Establish production standards and monitor performance against those standards
- Prepare cost estimates for projects and products
- Develop and implement process improvements to increase efficiency and reduce costs
- Maintain and troubleshoot existing equipment and systems
- Research and evaluate new technologies and equipment
- Develop and implement process improvements to increase efficiency and reduce costs
Education
Skills
owengreen@outlook.com
736-831-9407
Professional Summary
Employment history
- Research and evaluate new technologies and equipment
- Perform quality control and assurance tests
- Develop and implement maintenance plans
- Develop and implement safety and environmental policies
- Maintain and troubleshoot existing equipment and systems
- Create and maintain engineering documents, drawings, and specifications
- Design and develop new products and processes
- Train and mentor other engineers
- Develop and implement process improvements to increase efficiency and reduce costs
Education
Skills
ingram.cal@gmail.com
871-560-4005
Professional Summary
Employment history
- Develop and implement automation systems
- Develop and implement safety and environmental policies
- Train and mentor other engineers
- Develop and implement process improvements to increase efficiency and reduce costs
- Train and mentor other engineers
- Monitor and analyze production data to identify trends and areas for improvement
- Develop and implement automation systems
- Maintain and troubleshoot existing equipment and systems
- Analyze production processes and recommend improvements
Education
Skills
Not in love with this template? Browse our full library of resume templates
industrial engineer Job Descriptions; Explained
If you're applying for an industrial engineer position, it's important to tailor your resume to the specific job requirements in order to differentiate yourself from other candidates. Including accurate and relevant information that directly aligns with the job description can greatly increase your chances of securing an interview with potential employers.
When crafting your resume, be sure to use action verbs and a clear, concise format to highlight your relevant skills and experience. Remember, the job description is your first opportunity to make an impression on recruiters, so pay close attention to the details and make sure you're presenting yourself in the best possible light.
industrial engineer
- Provide technical expertise or support related to manufacturing.
- Review product designs for manufacture ability or completeness.
- Prepare documentation for new manufacturing processes or engineering procedures.
- To making sure that engineering and manufacturing processes are performed correctly using the right tools, materials and processes. An important part of the job involves designing the company’s quality standards and testing processes against those criteria.
- To prepare documents that provide requirements, specifications, guidelines, or characteristics that can be used consistently to ensure that materials, products, processes, and services are fit for their purpose.
- Prepare reports summarizing information or trends related to manufacturing performance.
industrial engineer
- Plan and establish sequence of operations to develop the garments and assemble parts and to promote efficient utilization.
- Draft and design layout of equipment, materials, and workspace to illustrate maximum efficiency.
- Develop manufacturing methods, labor utilization standards.
- Schedule deliveries based on production forecasts, material substitutions, storage and handling facilities, and maintenance requirements.
- By motivating the operators and developing the skill levels for factory efficiency.
industrial engineer
- Review production schedules, orders, and related information to obtain knowledge of manufacturing methods, procedures, and activities.
- Draft layout of equipment and work space to illustrate maximum efficiency using computer.
- Conduct Time and Motion Study.
- Submit monthly Improvement “Kaizen” report.
- Output monitoring and other clerical works.
industrial engineer
- Line balancing and allocate operators/machinesappropriately to various operations
- Preparing operation bulletin for all styles running in theplant
- Bottle neck clearing
- Time study, method study and ergonomics development
- Planning layouts
industrial engineer
- Quality Control CommitteeLead the team in deciding and implementing measures that will sustain and improve the quality of service of the company towards the clients.
- Creates Standard Operating Procedures (SOP) of the company.
- Audits the operation and facilities of the company.
- Solve the problems in the company through assessment and corrective and preventive action reports.
- Analyzes the proposed improvements in the operation and as well as in the system of the company
- Conducts training for the use of the system to the company.
industrial engineer Job Skills
For an industrial engineer position, your job skills are a key factor in demonstrating your value to the company and showing recruiters that you're the ight fit for the role. It's important to be specific when highlighting your skills and ensure that they are directly aligned with the job requirements, as this can greatly improve your chances of being hired. By showcasing your relevant skills and experience, you can make a compelling case for why you're the best candidate for the job.
How to include technical skills in your resume:
Technical skills are a set of specialized abilities and knowledge required to perform a particular job
effectively. Some examples of technical skills are data analysis, project management, software proficiency,
and programming languages, to name a few.
Add the technical skills that will get hired in your career
field with our simple-to-use resume builder. Select your desired resume template, once you reach the skills
section of the builder, manually write in the skill or simply click on "Add more skills". This will
automatically generate the best skills for your career field, choose your skill level, and hit "Save &
Next."
- 3D Printing
- CAD Software
- CNC Machining
- Lean Manufacturing
- Six Sigma
- Robotics
- Process Simulation
- Quality Control
- Automation
- Prototype Development
- PLC Programming
- Statistical Analysis
- Design of Experiments
- Ergonomics
- Project Management
- Manufacturing Processes
- Troubleshooting
- Material Handling
- Supply Chain Management
- Cost Estimation.
How to include soft skills in your resume:
Soft skills are non-technical skills that relate to how you work and that can be used in any job. Including
soft skills such as time management, creative thinking, teamwork, and conflict resolution demonstrate your
problem-solving abilities and show that you navigate challenges and changes in the workplace
efficiently.
Add competitive soft skills to make your resume stand-out to recruiters! Simply select
your preferred resume template in the skills section, enter the skills manually or use the "Add more skills"
option. Our resume builder will generate the most relevant soft skills for your career path. Choose your
proficiency level for each skill, and then click "Save & Next" to proceed to the next section.
- Communication
- Interpersonal
- Leadership
- Time Management
- Problem Solving
- Decision Making
- Critical Thinking
- Creativity
- Adaptability
- Teamwork
- Organization
- Planning
- Public Speaking
- Negotiation
- Conflict Resolution
- Research
- Analytical
- Attention to Detail
- Self-Motivation
- Stress Management
- Collaboration
- Coaching
- Mentoring
- Listening
- Networking
- Strategic Thinking
- Negotiation
- Emotional Intelligence
- Adaptability
- Flexibility
- Reliability
- Professionalism
- Computer Literacy
- Technical
- Data Analysis
- Project Management
- Customer Service
- Presentation
- Written Communication
- Social Media
- Troubleshooting
- Quality Assurance
- Collaboration
- Supervisory
- Risk Management
- Database Management
- Training
- Innovation
- Documentation
- Accounting
- Financial Management
- Visualization
- Reporting
- Business Acumen
- Process Improvement
- Documentation
- Relationship Management.
How to Improve Your industrial engineer Resume
Navigating resume pitfalls can mean the difference between landing an interview or not. Missing job descriptions or unexplained work history gaps can cause recruiters to hesitate. Let's not even talk about the impact of bad grammar, and forgetting your contact info could leave your potential employer hanging. Aim to be comprehensive, concise, and accurate.
Professional Summary
Employment history
- Develop and implement safety and environmental policies
- Design and develop new products and processes
- Maintain and troubleshoot existing equipment and systems
- Develop and implement automation systems
- Maintain and troubleshoot existing equipment and systems
- Establish production standards and monitor performance against those standards
Education
Skills
Include your Contact Information and Job Descriptions
Missing job descriptions lessens your chances of getting hired.
Key Insights- Employers want to know what you've accomplished, so make sure to include descriptions for all of your previous jobs.
- Keep job descriptions short but don't just list your jobs.
- Never copy-paste a job description to post on your resume. Get inspired and use tools to help you write customized descriptions.
How to Optimize Your industrial engineer Resume
Keep an eye out for these resume traps. Neglecting to detail your job roles or explain gaps in your career can lead to unnecessary doubts. Grammar blunders can reflect negatively on you, and without contact information, how can employers reach you? Be meticulous and complete.
nelson_bernie@protonmail.com
945-621-6301
Employment history
- Maintane and troubleshoot exsisting equipement and systemes.
- Analysse production proccesses and recomend improovments.
- Establishs production standerds and monitors performance aginst thoses standerds.
- Develp annd impplement saffety annd environmmental pooliciess.
- Trane and menthor othar engineers.
- Develp, and implementt maintenence planss.
- Manege n' coordinate projecs.
- Develp and implemet saftey and enviromental policys.
- Trainnd mentor othher engineerss.
Education
Skills
Correct Grammar and Address Gap Years in Your Resume
Don't leave unexplained gaps in your work history.
Key Insights- When explaining gaps in your employment section, start by being honest.
- Elaborate on the gap and show that you never stopped learning.
- Explain and elaborate any gap in your work history by highlighting new skills.
industrial engineer Cover Letter Example
A cover letter can be a valuable addition to your job application when applying for an industrial engineer position. Cover letters provide a concise summary of your qualifications, skills, and experience, also it also gives you an opportunity to explain why you're the best fit for the job. Crafting a cover letter that showcases your relevant experience and enthusiasm for the Accounts Payable role can significantly improve your chances of securing an interview.
Griffin karlgriffin57@aol.com
981-848-8056
420 Creek Drive, Vernon Center, MN
56090
Amazon
Seattle, Washington
To Whom It May Concern
I am a highly motivated and experienced Industrial Engineer with 4 years of experience in Engineering. I am excited to apply for the Senior Industrial Engineer position at Amazon, where I am confident that I can contribute to your organization's success.
As someone who has always been committed to making a positive impact on the world, I have pursued opportunities to contribute to my community through my work wherever I may be. My experience in this field has equipped me with the skills and knowledge necessary to succeed throughout my life and I am confident that they will help me to bring my passion and expertise to your organization and help drive your success.
Thank you for considering my application for the Senior Industrial Engineer role. I am looking forward to a future where we work together to drive this organization's success.
Kindest regards,
Karl Griffin
981-848-8056
karlgriffin57@aol.com
Karl Griffin
Showcase your most significant accomplishments and qualifications with this cover
letter.
Personalize this cover letter in just few minutes with our user-friendly tool!
Related Resumes & Cover Letters
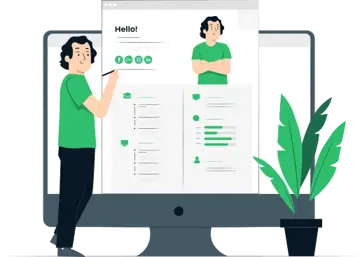
Build your Resume in 15 minutes
Create an awesome resume that meets the expectations of potential employers with our selection of professional, field-tested resume templates.