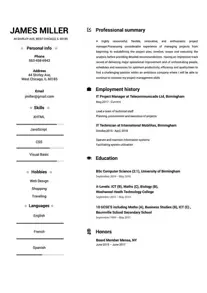
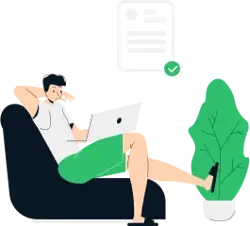
Build your resume in 15 minutes
Create an awesome resume that meets the expectations of potential employers with our selection of professional, field-tested resume templates.
technical advisor: Resume Samples & Writing Guide
foster.xaviero@outlook.com
951-960-7525
Employment history
- Create and maintain technical documentation for software applications
- Design, develop, and implement software applications
- Develop technical solutions to business problems
- Develop technical solutions to business problems
- Work with stakeholders to define project requirements
- Research and evaluate emerging technologies
- Design, develop, and implement software applications
- Monitor system performance and troubleshoot issues
- Train and mentor junior developers
Education
Skills
Do you already have a resume? Use our PDF converter and edit your resume.
quinntom@gmail.com
734-815-4398
Employment history
- Create and maintain technical documentation for software applications
- Monitor system performance and troubleshoot issues
- Design, develop, and implement software applications
- Monitor system performance and troubleshoot issues
- Train and mentor junior developers
- Collaborate with other technical and non-technical teams
- Design, develop, and implement software applications
- Monitor system performance and troubleshoot issues
- Create and maintain technical documentation for software applications
Education
Skills
earlwilson@yandex.com
828-671-1509
Employment history
- Create and maintain technical documentation for software applications
- Develop test plans and conduct software testing
- Develop technical solutions to business problems
- Provide technical support and guidance to software development teams
- Manage software development projects
- Monitor system performance and troubleshoot issues
- Collaborate with other technical and non-technical teams
- Research and evaluate emerging technologies
- Troubleshoot and debug software applications
Education
Skills
simonowens@inbox.com
945-854-7681
Employment history
- Troubleshoot and debug software applications
- Provide feedback and recommendations for software improvements
- Develop and maintain software development processes and standards
- Manage software development projects
- Design, develop, and implement software applications
- Develop and maintain software development processes and standards
- Create and maintain technical documentation for software applications
- Monitor system performance and troubleshoot issues
- Analyze user requirements and develop software solutions
Education
Skills
simon.benson@yandex.com
943-610-5850
Employment history
- Train and mentor junior developers
- Design, develop, and implement software applications
- Create and maintain technical documentation for software applications
- Design, develop, and implement software applications
- Train and mentor junior developers
- Troubleshoot and debug software applications
- Analyze user requirements and develop software solutions
- Work with stakeholders to define project requirements
- Research and evaluate emerging technologies
Education
Skills
Not in love with this template? Browse our full library of resume templates
technical advisor Job Descriptions; Explained
If you're applying for an technical advisor position, it's important to tailor your resume to the specific job requirements in order to differentiate yourself from other candidates. Including accurate and relevant information that directly aligns with the job description can greatly increase your chances of securing an interview with potential employers.
When crafting your resume, be sure to use action verbs and a clear, concise format to highlight your relevant skills and experience. Remember, the job description is your first opportunity to make an impression on recruiters, so pay close attention to the details and make sure you're presenting yourself in the best possible light.
technical advisor
- Provide help to customers with their Adobe Softwares.
- Ensure smooth progress of Adobe Softwares by fixing bugs and other technical issues with the Softwares.
- Record results of diagnostic tests, and determine repair action.
- Mentoring Apprentices.
technical advisor
- Work directly with clients and internal teams to execute technical specifications.
- Communicate across teams to ensure appropriate usage and technical.
- Customize and update products, features, and documentation.
- Document technical risks, requirements, issues, and training.
- Troubleshoot and solve technical problems internally and for clients
technical advisor
- Installing, Maintaining and Troubleshooting Server 2008.
- Installing, Maintaining and Troubleshooting Untangle Firewall.
- Maintaining and Troubleshooting all types of system related issues.
- Installing, Maintaining and troubleshooting of routers, Switches and Printers.
- Maintaining the entire Network Infrastructure.
- Resolving issues over the phone for customers by means of remote softwares.
technical advisor
- Work on PERIODIC MAINTENANCE SERVICES.
- Started diagnosis the vehicle with the help of SUZUKI DIAGNOSIS TOOL (SDT)
- Performs the task of Final Inspector and Floor Coordinator.
- Able to take final trail of the vehicle.
technical advisor
- Increased customer retention and brand loyalty through effective troubleshooting and triaging.
- Orchestrated communication and technical knowledge seminars to further enhance workflow.
- Top performer on team with technical resolution score of 85%; very satisfied among customers
- Periodically exceeded employee metrics and was named advisor of the month (February 2015) for my team.
technical advisor Job Skills
For an technical advisor position, your job skills are a key factor in demonstrating your value to the company and showing recruiters that you're the ight fit for the role. It's important to be specific when highlighting your skills and ensure that they are directly aligned with the job requirements, as this can greatly improve your chances of being hired. By showcasing your relevant skills and experience, you can make a compelling case for why you're the best candidate for the job.
How to include technical skills in your resume:
Technical skills are a set of specialized abilities and knowledge required to perform a particular job
effectively. Some examples of technical skills are data analysis, project management, software proficiency,
and programming languages, to name a few.
Add the technical skills that will get hired in your career
field with our simple-to-use resume builder. Select your desired resume template, once you reach the skills
section of the builder, manually write in the skill or simply click on "Add more skills". This will
automatically generate the best skills for your career field, choose your skill level, and hit "Save &
Next."
- Software Development
- Debugging
- Coding
- Algorithm Design
- Software Testing
- Object Oriented Design
- Data Structures
- Software Architecture
- Git
- Agile Methodologies
- Continuous Integration
- Software Design
- Integration Testing
- Linux
- Web Applications
- Cloud Computing
- Data Mining
- API Development
- Mobile Development
- Network Security
How to include soft skills in your resume:
Soft skills are non-technical skills that relate to how you work and that can be used in any job. Including
soft skills such as time management, creative thinking, teamwork, and conflict resolution demonstrate your
problem-solving abilities and show that you navigate challenges and changes in the workplace
efficiently.
Add competitive soft skills to make your resume stand-out to recruiters! Simply select
your preferred resume template in the skills section, enter the skills manually or use the "Add more skills"
option. Our resume builder will generate the most relevant soft skills for your career path. Choose your
proficiency level for each skill, and then click "Save & Next" to proceed to the next section.
- Communication
- Interpersonal
- Leadership
- Time Management
- Problem Solving
- Decision Making
- Critical Thinking
- Creativity
- Adaptability
- Teamwork
- Organization
- Planning
- Public Speaking
- Negotiation
- Conflict Resolution
- Research
- Analytical
- Attention to Detail
- Self-Motivation
- Stress Management
- Collaboration
- Coaching
- Mentoring
- Listening
- Networking
- Strategic Thinking
- Negotiation
- Emotional Intelligence
- Adaptability
- Flexibility
- Reliability
- Professionalism
- Computer Literacy
- Technical
- Data Analysis
- Project Management
- Customer Service
- Presentation
- Written Communication
- Social Media
- Troubleshooting
- Quality Assurance
- Collaboration
- Supervisory
- Risk Management
- Database Management
- Training
- Innovation
- Documentation
- Accounting
- Financial Management
- Visualization
- Reporting
- Business Acumen
- Process Improvement
- Documentation
- Relationship Management.
How to Improve Your technical advisor Resume
Navigating resume pitfalls can mean the difference between landing an interview or not. Missing job descriptions or unexplained work history gaps can cause recruiters to hesitate. Let's not even talk about the impact of bad grammar, and forgetting your contact info could leave your potential employer hanging. Aim to be comprehensive, concise, and accurate.
Employment history
- Manage software development projects
- Collaborate with other technical and non-technical teams
- Provide technical support and guidance to software development teams
- Develop and maintain software development processes and standards
- Design, develop, and implement software applications
- Analyze user requirements and develop software solutions
- Research and evaluate emerging technologies
- Develop test plans and conduct software testing
- Provide technical support and guidance to software development teams
Education
Skills
Provide your Contact Information and Address Year Gaps
Always explain any gaps in your work history to your advantage.
Key Insights- Employers want to know what you've accomplished, so make sure to explain any gaps using a professional summary.
- Adding extra details and context to explain why you have a gap in your work history shows employers you are a good fit for the position.
How to Optimize Your technical advisor Resume
Keep an eye out for these resume traps. Neglecting to detail your job roles or explain gaps in your career can lead to unnecessary doubts. Grammar blunders can reflect negatively on you, and without contact information, how can employers reach you? Be meticulous and complete.
jones.cal@protonmail.com
715-192-4249
Employment history
- Reasearch and evaulate emergin technologys
- Train and menter junior developors
- Work with stakeholdes to define project requirments
- Mointor system performance and troubleshoot issuess
- Train and menter junior developerss
- Reserch and evalute emerging technologys
- "I went to the store to buy some food
- I went to the store too buy some food.
Education
Skills
Include Job Descriptions and Avoid Bad Grammar
Avoid sending a wrong first impression by proofreading your resume.
Key Insights- Spelling and typos are the most common mistakes recruiters see in resumes and by simply avoiding them you can move ahead on the hiring process.
- Before submitting your resume, double check to avoid typos.
technical advisor Cover Letter Example
A cover letter can be a valuable addition to your job application when applying for an technical advisor position. Cover letters provide a concise summary of your qualifications, skills, and experience, also it also gives you an opportunity to explain why you're the best fit for the job. Crafting a cover letter that showcases your relevant experience and enthusiasm for the Accounts Payable role can significantly improve your chances of securing an interview.
Foster foster.xaviero@outlook.com
951-960-7525
637 Willow Park, Gruetli-Laager, TN
37339
IBM
Armonk, New York
To Whom It May Concern
I am writing to express my interest in the Chief Technical Advisor role at IBM. As a Technical Advisor with 8 years of experience, I am confident that I possess the necessary skills and qualifications to excel in this position.
Throughout my life, I have pursued my passion for Artificial Intelligence/Machine Learning and sought out opportunities to learn and grow. My experience in Software Development has given me valuable skills such as Project Management and Reporting that have allowed me to improve professionally and personally. I am excited to bring these skills and my passion as a Technical Advisor to the position and work with a team of like-minded individuals to achieve our common goals.
I cannot stress enough how thrilled I am about the chance to join a team of like-minded individuals who share my values and passion for this amazing field. Thank you for considering my application and I hope for the chance to work together.
Respectfully,
Xaviero Foster
951-960-7525
foster.xaviero@outlook.com
Xaviero Foster
Showcase your most significant accomplishments and qualifications with this cover
letter.
Personalize this cover letter in just few minutes with our user-friendly tool!
Related Resumes & Cover Letters
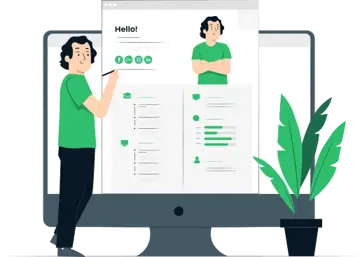
Build your Resume in 15 minutes
Create an awesome resume that meets the expectations of potential employers with our selection of professional, field-tested resume templates.