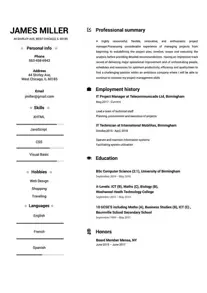
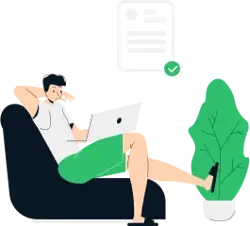
Build your resume in 15 minutes
Create an awesome resume that meets the expectations of potential employers with our selection of professional, field-tested resume templates.
maintenance planner: Resume Samples & Writing Guide
wilson-roy@icloud.com
952-017-1997
Professional Summary
Employment history
- Assist with budgeting and cost control
- Develop and implement preventive maintenance plans
- Train and mentor maintenance staff
- Monitor and maintain inventory of spare parts
- Perform root cause analysis for equipment failures
- Develop and implement preventive maintenance plans
- Assist with budgeting and cost control
- Train and mentor maintenance staff
- Identify and order necessary parts and supplies
Education
Skills
Do you already have a resume? Use our PDF converter and edit your resume.
bradhawkins@zoho.com
760-832-2605
Professional Summary
Employment history
- Train and mentor maintenance staff
- Develop and implement strategies to reduce downtime
- Develop and implement continuous improvement initiatives
- Schedule and coordinate maintenance activities
- Monitor and manage maintenance work orders
- Ensure compliance with safety regulations
- Assist with budgeting and cost control
- Develop and implement continuous improvement initiatives
- Identify and order necessary parts and supplies
Education
Skills
ernestowens68@protonmail.com
850-603-4840
Employment history
- Analyze equipment performance data
- Monitor and maintain inventory of spare parts
- Track and report on maintenance activities
- Monitor and maintain inventory of spare parts
- Train and mentor maintenance staff
- Ensure compliance with safety regulations
- Develop and implement strategies to reduce downtime
- Schedule and coordinate maintenance activities
- Train and mentor maintenance staff
Education
Skills
edwards-abe@gmail.com
782-240-4910
Professional Summary
Employment history
- Analyze equipment performance data
- Identify and order necessary parts and supplies
- Monitor and maintain inventory of spare parts
- Schedule and coordinate maintenance activities
- Analyze equipment performance data
- Ensure compliance with safety regulations
- Develop and implement strategies to reduce downtime
- Schedule and coordinate maintenance activities
- Ensure compliance with safety regulations
Education
Skills
waltroberts80@outlook.com
972-592-5218
Employment history
- Develop and implement preventive maintenance plans
- Ensure compliance with safety regulations
- Establish and maintain strong relationships with vendors
- Ensure compliance with safety regulations
- Develop and implement strategies to reduce downtime
- Schedule and coordinate maintenance activities
- Track and report on maintenance activities
- Develop and implement preventive maintenance plans
- Identify and order necessary parts and supplies
Education
Skills
Not in love with this template? Browse our full library of resume templates
maintenance planner Job Descriptions; Explained
If you're applying for an maintenance planner position, it's important to tailor your resume to the specific job requirements in order to differentiate yourself from other candidates. Including accurate and relevant information that directly aligns with the job description can greatly increase your chances of securing an interview with potential employers.
When crafting your resume, be sure to use action verbs and a clear, concise format to highlight your relevant skills and experience. Remember, the job description is your first opportunity to make an impression on recruiters, so pay close attention to the details and make sure you're presenting yourself in the best possible light.
maintenance planner / scheduler
- Collaborated with team to define business requirements for organizational processes, achieve productivity standards and adhere to accuracy standards
- Developed team communications and information for [Type] meetings
- Developed product and solution positioning, messaging by prospective buyer role and methods to overcome competitive objections
- Created scheduling reports in DMS system to efficiently and effectively move product and adhere to shipping commitments
- Conducted field visits and met corporate customers for business development
- Managed high-value existing and new business partnerships to deliver on objectives and maximize corporate revenue, support and awareness
- Saved $[Amount] by researching and implementing [Type] cost-saving initiatives and creating fresh new approaches to long-standing problems
maintenance planner
- Welcomed visitors to office, communicated arrival to team and managed visit expectations
- Managed quality assurance program including on site evaluations, internal audits and customer surveys
- Followed quality standards and procedures to minimize shipment errors and maximize customer satisfaction
- Conducted office management and emergency preparedness orientation to provide special skills and test specific emergency plan components
maintenance planner
- Plan and schedule maintenance tasks for the week.
- Record and manage equipment downtime on CMMS database.
- Follow-up with Supervisors/Managers to ensure compliance of scheduled tasks.
- Material planning for planned tasks – weekly, monthly and yearly .
- Prepare daily equipment downtime and availability.
- Prepare monthly report summarizing material and labour cost; equipment availability and reliability.
- Collaborate with other departments to ensure scheduled tasks are executed.
maintenance planner
- Updated quality control standard methods and procedures to meet customer SLA and compliance requirements
- Complied with safety and hazardous material handling, storage regulatory requirements and internal procedures affecting business operations
- Improved quality processes for increased efficiency and effectiveness
- Supervised and led employees to high performance levels in cross-functional matrix management structure
- Identified and resolved process issues to encourage smoother procedures, more efficient workflow and overall business growth
- Adhered to established policies, procedures and compliance for satisfactory audit rating
- Sorted incoming mail and faxes and expedited urgent correspondence for immediate attention
maintenance planner / scheduler Job Skills
For an maintenance planner / scheduler position, your job skills are a key factor in demonstrating your value to the company and showing recruiters that you're the ight fit for the role. It's important to be specific when highlighting your skills and ensure that they are directly aligned with the job requirements, as this can greatly improve your chances of being hired. By showcasing your relevant skills and experience, you can make a compelling case for why you're the best candidate for the job.
How to include technical skills in your resume:
Technical skills are a set of specialized abilities and knowledge required to perform a particular job
effectively. Some examples of technical skills are data analysis, project management, software proficiency,
and programming languages, to name a few.
Add the technical skills that will get hired in your career
field with our simple-to-use resume builder. Select your desired resume template, once you reach the skills
section of the builder, manually write in the skill or simply click on "Add more skills". This will
automatically generate the best skills for your career field, choose your skill level, and hit "Save &
Next."
- PLC Programming
- Equipment Maintenance
- Troubleshooting
- Welding
- Hydraulics
- Pneumatics
- Preventive Maintenance
- Electrical Systems
- Machine Operation
- CNC Programming
- CAD/CAM
- Fabrication
- Machining
- Inspection
- Automation
- Quality Control
- Root Cause Analysis
- HVAC
- Safety Protocols
- Automotive Repair
How to include soft skills in your resume:
Soft skills are non-technical skills that relate to how you work and that can be used in any job. Including
soft skills such as time management, creative thinking, teamwork, and conflict resolution demonstrate your
problem-solving abilities and show that you navigate challenges and changes in the workplace
efficiently.
Add competitive soft skills to make your resume stand-out to recruiters! Simply select
your preferred resume template in the skills section, enter the skills manually or use the "Add more skills"
option. Our resume builder will generate the most relevant soft skills for your career path. Choose your
proficiency level for each skill, and then click "Save & Next" to proceed to the next section.
- Communication
- Interpersonal
- Leadership
- Time Management
- Problem Solving
- Decision Making
- Critical Thinking
- Creativity
- Adaptability
- Teamwork
- Organization
- Planning
- Public Speaking
- Negotiation
- Conflict Resolution
- Research
- Analytical
- Attention to Detail
- Self-Motivation
- Stress Management
- Collaboration
- Coaching
- Mentoring
- Listening
- Networking
- Strategic Thinking
- Negotiation
- Emotional Intelligence
- Adaptability
- Flexibility
- Reliability
- Professionalism
- Computer Literacy
- Technical
- Data Analysis
- Project Management
- Customer Service
- Presentation
- Written Communication
- Social Media
- Troubleshooting
- Quality Assurance
- Collaboration
- Supervisory
- Risk Management
- Database Management
- Training
- Innovation
- Documentation
- Accounting
- Financial Management
- Visualization
- Reporting
- Business Acumen
- Process Improvement
- Documentation
- Relationship Management.
How to Improve Your maintenance planner / scheduler Resume
Navigating resume pitfalls can mean the difference between landing an interview or not. Missing job descriptions or unexplained work history gaps can cause recruiters to hesitate. Let's not even talk about the impact of bad grammar, and forgetting your contact info could leave your potential employer hanging. Aim to be comprehensive, concise, and accurate.
Employment history
- Develop and implement continuous improvement initiatives
- Establish and maintain strong relationships with vendors
- Schedule and coordinate maintenance activities
Education
Skills
Provide your Contact Information and Address Year Gaps
Always explain any gaps in your work history to your advantage.
Key Insights- Employers want to know what you've accomplished, so make sure to explain any gaps using a professional summary.
- Adding extra details and context to explain why you have a gap in your work history shows employers you are a good fit for the position.
How to Optimize Your maintenance planner / scheduler Resume
Keep an eye out for these resume traps. Neglecting to detail your job roles or explain gaps in your career can lead to unnecessary doubts. Grammar blunders can reflect negatively on you, and without contact information, how can employers reach you? Be meticulous and complete.
paulvaughn86@protonmail.com
725-310-4094
Professional Summary
Employment history
- Idintify and order neccessary parts and suplies
- Monitor an manage maintenance work orders
- Track an report on maintenace activities
- Ensure complience with saftey regulations
- Assit with budgetting and cost control
- Develp and impliment preventative maintanence plans
- "I went to the store to buy some food
- I went too the store too buy some food.
Education
Skills
Include Job Descriptions and Avoid Bad Grammar
Avoid sending a wrong first impression by proofreading your resume.
Key Insights- Spelling and typos are the most common mistakes recruiters see in resumes and by simply avoiding them you can move ahead on the hiring process.
- Before submitting your resume, double check to avoid typos.
maintenance planner / scheduler Cover Letter Example
A cover letter can be a valuable addition to your job application when applying for an maintenance planner / scheduler position. Cover letters provide a concise summary of your qualifications, skills, and experience, also it also gives you an opportunity to explain why you're the best fit for the job. Crafting a cover letter that showcases your relevant experience and enthusiasm for the Accounts Payable role can significantly improve your chances of securing an interview.
Wilson wilson-roy@icloud.com
952-017-1997
203 Pinecrest Avenue, Cream Ridge, NJ
08514
United Technologies
Farmington, Connecticut
Dear Hiring Committee
I am a results-driven Maintenance Planner with 12 years of experience in Maintenance & Repair. I am excited to submit my application for the Chief Maintenance Planner role at United Technologies, where I believe I can make a valuable contribution to your team.
Growing up, I always had a fascination with Equipment Maintenance. As I pursued my education and gained experience in this field, I realized that this was where I could make the most impact. I have had the opportunity to work on things throughout my career like personal projects and voluntary work, which have developed in me a deep understanding of the challenges and opportunities in this field. I am excited to bring my passion and expertise to the role at and help your organization achieve its goals.
I appreciate the opportunity to apply for the Chief Maintenance Planner position. I am committed to making a positive impact on the world, so I am thrilled about the opportunity to join your team and work towards achieving our shared goals for the betterment of everyone.
Best regards,
Roy Wilson
952-017-1997
wilson-roy@icloud.com
Roy Wilson
Showcase your most significant accomplishments and qualifications with this cover
letter.
Personalize this cover letter in just few minutes with our user-friendly tool!
Related Resumes & Cover Letters
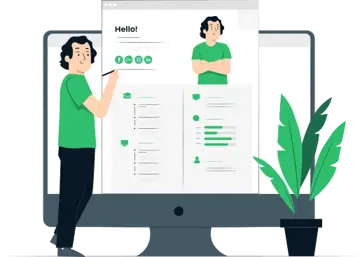
Build your Resume in 15 minutes
Create an awesome resume that meets the expectations of potential employers with our selection of professional, field-tested resume templates.